Arkema, a world leader in specialty materials, will introduce the latest developments in more sustainable solutions for lower-energy intensive energy curing systems at RadTech UV+EB, May 20–22, 2024, in Orlando, Florida, at booth 301. During the technical conferences, Arkema experts will present research in UV-LED-EB sustainable materials for coatings, graphic arts, battery and 3D printing applications.
The market needs material solutions that enhance the sustainability and performance of energy curing applications.
These include eliminating substances of concern and reducing VOCs, using lower carbon and more circular feedstocks, lowering energy intensity in application, doing more with less and making it easier to recycle materials - all while maintaining durable product performance.
Attendees can learn about these new sustainable material innovations for SARTOMER® UV/LED/EB-curable specialty resin and N3XTDIMENSION® 3D printing product lines.
REMOVING SUBSTANCES OF CONCERN
- Reactive resins for low extractables and migration: Material advancements to reduce migration potential and further improve safety and performance in packaging inks and coatings.
LOWER CARBON AND MORE CIRCULAR FEEDSTOCKS
- Bio-based (meth)acrylate solutions, based on segregated feedstock, contain up to 88% bio-content. Arkema is introducing two new difunctional oligomers for 3D printing applications. SARBIO® 7405, toughening oligomer, contains 50% bio-content and brings an excellent balance between hardness and flexibility. SARBIO® 7407, highly flexible oligomer, contains 75% bio-content and enables high elastomeric performance.
- Bio-attributed mass balance resins: Arkema announced Its first ISCC+ certification for UV-LED-EB solutions at Villers-Saint-Paul, France. This marks the first step in its ambition to further certify UV-LED-EB manufacturing sites in US and China.
LOWER ENERGY INTENSITY
- UV/EB-cured solutions for coil coatings: Most recent material solutions to enable a technology transition for up 60% energy savings* in application, contributing to decarbonize the built environment.
- Dielectric coatings for battery cells: Solvent-free and lower energy-intensive UV-curable resins and photoinitiators enable excellent dielectric properties, adhesion, flexibility and ease of assembly.
*ECCA - Zero Carbon Coil Coating Line – The Way Forward
END OF LIFE MANAGEMENT - EASING RECYCLABILITY
- De-inking solutions for UV printed inks: New approach to enable recyclability of plastic substrates with or without a removable primer. This innovation supports our customers in their journey to a more sustainable future and enables more versatility in product development for the recycling of plastics.
TECHNICAL CONFERENCE PROGRAM
A More Sustainable Process for Dispersing Core Shell Impact Modifiers in Hydrophobic Acrylic Monomers
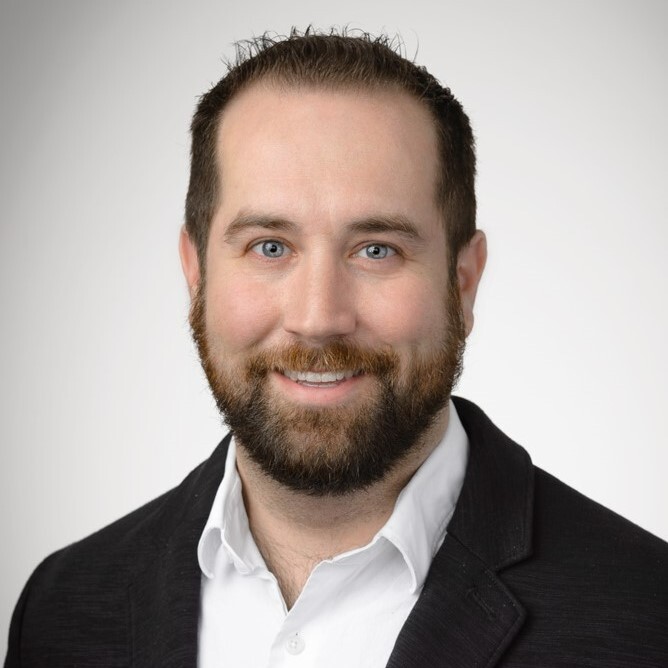
The Future of Sustainability in Additive Manufacturing
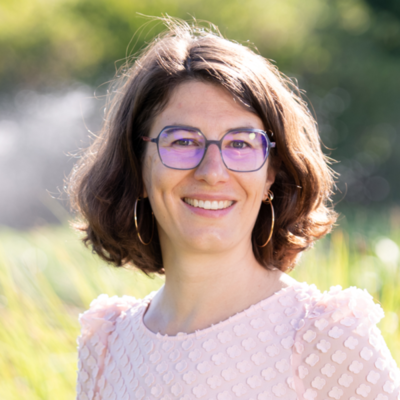
Enable Recyclability of Packaging with De-inking solutions for UV printed inks
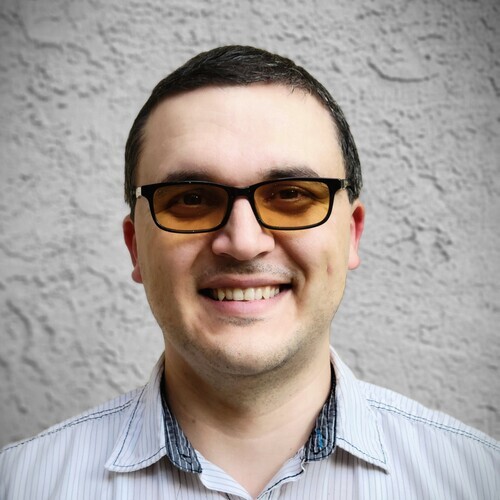
Energy-Efficient Insulative Coatings for Battery Cell Applications
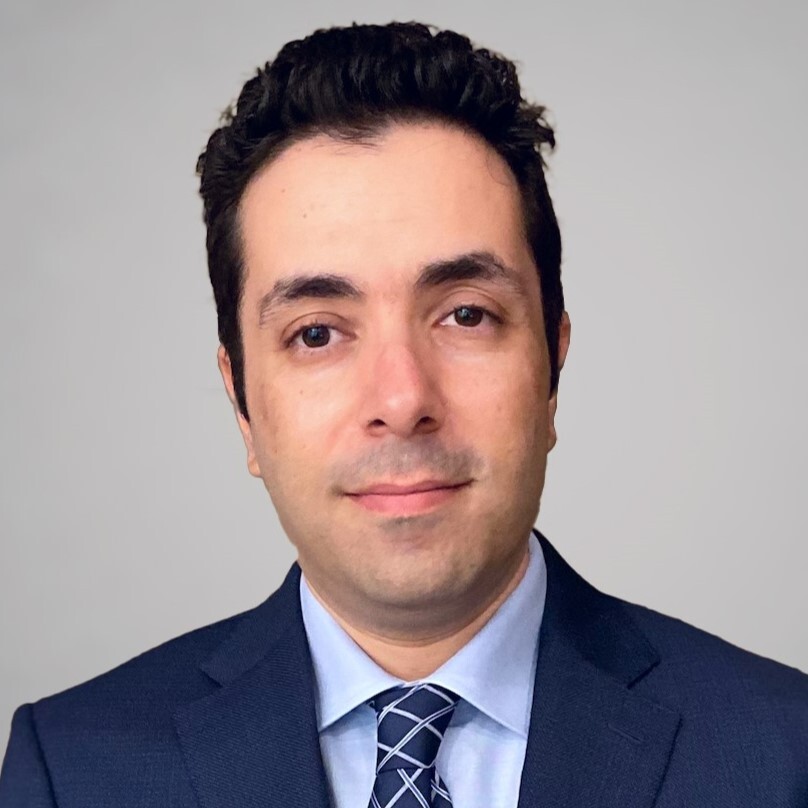
Inherently Reactive Urethane Acrylate Oligomers for UV-cured Materials with Low Extractables
Reactive Acrylic Copolymers for use in Low Extractable Coatings
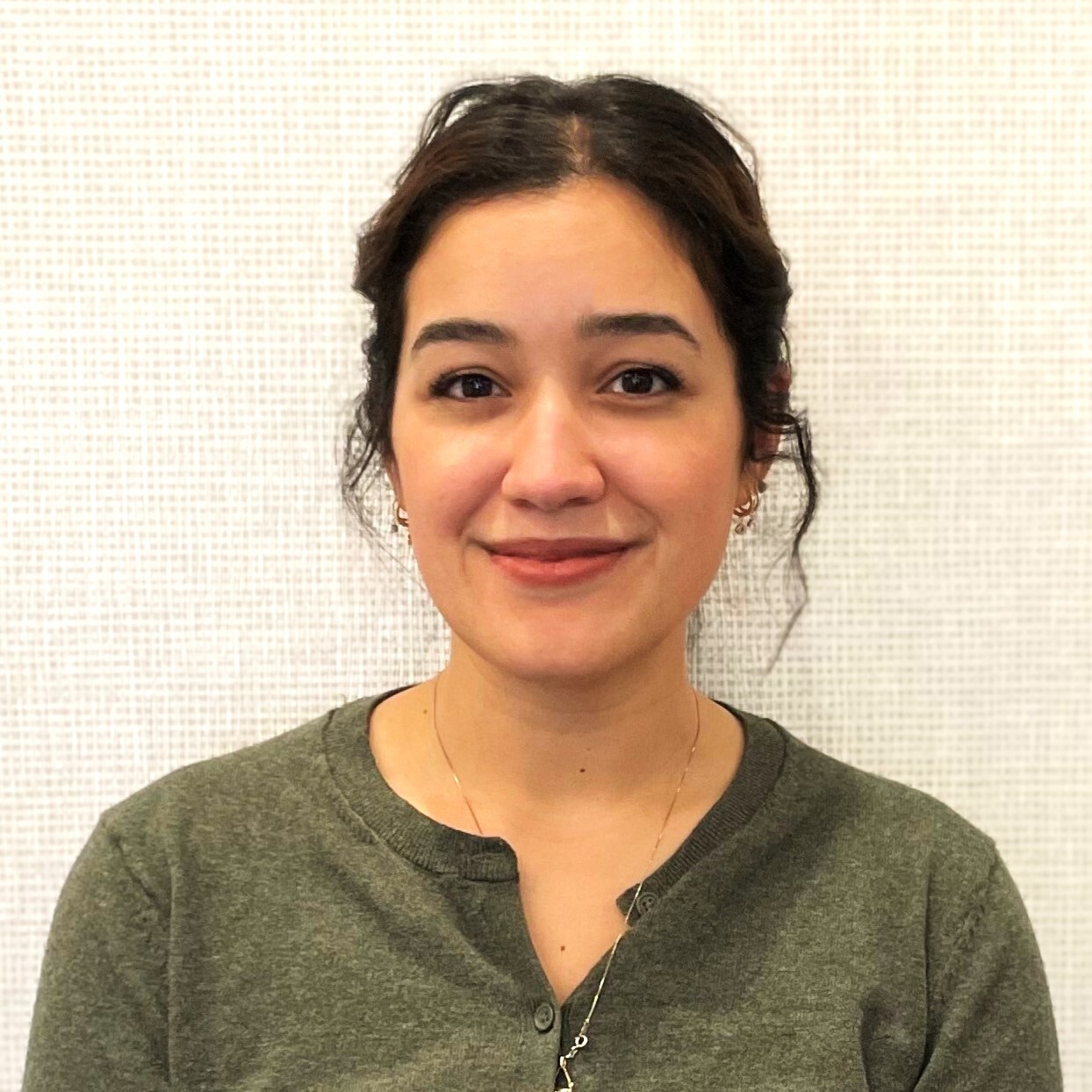